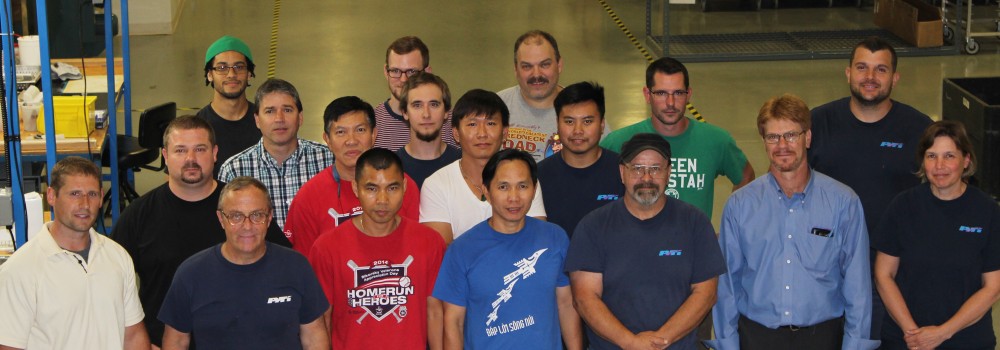
Manufacturers are increasingly choosing adhesive bonding as the preferred method for joining components due to its many advantages over traditional joining methods. Adhesive bonding is a critical process and if done improperly can lead to system failures. Proper bonding techniques start with understanding the process requirements, properly maintaining your bond facility and inventory, and having highly trained operators to carry out the requirements.
PTI Industries Adhesive Bonding Department’s team of experts’ goal is to maintain compliance to all bonding process requirements to ensure your critical adhesive bonding needs.
How the department is organized
PTI’s Adhesive Bonding Department is organized by the different types of adhesive bonding methods and spec requirements for controlled areas. There are two contamination controlled areas that are maintained for temperature, humidity, and positive pressure. One area is for RTV (Room Temperature Vulcanizing) bonding, and the second is for epoxy bonding used in applications such as liner (metal to metal) and Teflon bonding. There are also additional environmentally maintained areas for other methods and specifications, such as magnesium bonding.
Maintaining contamination control areas
Calibrated controls for temperature and humidity are checked twice a day to ensure an acceptable specification range is met. Humidifiers and dehumidifiers maintain the proper humidity levels for effective adhesive bonding.
Approval processing for the right adhesive method
Each adhesive bonding method is specification driven and controlled. Nearly all prime manufacturers require approvals for the type of bonding that is required in the form of an overall approval for processing. They also may require specific approvals in the form of a technical plan or process plan for the parts being processed or the method of processing.
Getting the right fixtures and tooling
PTI determines the appropriate bonding tooling and fixtures required for each specific job. Tooling is designed and created by our bond technical leader, quality department and engineering department. Most tooling or fixtures can be made onsite in our machine shop.
Adhesive storage and quality control
PTI stores adhesives in three ways:
1. Room temperature cabinets
2. Refrigerators
3. Freezer
All storage options are quality controlled. The refrigerators and freezer are monitored with state of the art thermocouple chart recorders. The freezer is set with an alarm indicating variation above or below the acceptable temperature range. When technicians aren’t on site, any deviation is sent to PTI’s security company, who then notifies PTI.
Typical adhesive shelf life can range from six months to one year. Shelf life is monitored with an inventory control system that includes product labels and an online tracking system. All out time of adhesives are tracked and recorded.
Your Certificate of Conformance
PTI provides a certificate of conformance for all jobs and for all special processes in our support services as part of our quality assurance program.
Who works in PTI’s Adhesive Bonding Department?
The Adhesive Bonding Department team includes a Bond Manager, Bond Technical Leader/Expert, two Team Leaders, Expeditor, Quality Engineer, and Bond Operators/Technicians.
All team members undergo on-the-job training on systems, procedures, and processing. Classroom training, special program training, part and job specific training are done by the quality department, bond technical leader, team leaders and high level operators.
For any questions on PTI’s adhesive bonding special processes, please contact Jessica Taylor.